Conveyor metal detectors have become an essential tool in enhancing industrial safety across various sectors. These detectors are designed to identify and remove metallic contaminants from products as they move along a conveyor belt, ensuring that they meet safety and quality standards. In this article, we will explore the importance of conveyor metal detectors in industrial safety and how they contribute to creating a safer working environment.
Enhancing industrial safety with conveyor metal detectors involves implementing these devices along conveyor systems to identify and remove metal contaminants from products as they move through the production process. This can help prevent injury to workers and damage to equipment, as well as ensure compliance with safety and quality standards. Conveyor metal detectors can be customized to suit specific applications and integrated seamlessly into existing manufacturing processes. They are an effective tool for enhancing safety and productivity in industrial environments.
10 Benefits of Using a Conveyor Metal Detector in Food Processing
conrad gr 3 plus
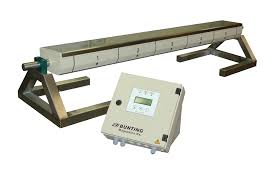
1. Improved Food Safety: Conveyor metal detectors can help prevent contamination of food products by identifying and removing metal contaminants before they reach the consumer. 2. Compliance with Regulations: Using a conveyor metal detector can help food processing facilities comply with food safety regulations and standards set by regulatory agencies. 3. Reduced Product Waste: Implementing a metal detector can help reduce product waste by detecting and removing contaminated products before they are packaged and shipped. 4. Protects Equipment: Metal contaminants in food products can damage processing equipment, leading to costly repairs and downtime. Using a conveyor metal detector can help protect machinery from damage. 5. Enhanced Brand Reputation: Food processing facilities that prioritize food safety initiatives and invest in metal detection technology can build a positive brand reputation for producing safe and high-quality products. 6. Cost Savings: By reducing product waste and minimizing the risk of equipment damage, conveyor metal detectors can contribute to cost savings for food processing operations. 7. Increased Efficiency: Integrating a metal detector into the production line can improve efficiency by automating the detection and removal of metal contaminants from the food processing process. 8. Versatile Applications: Conveyor metal detectors are suitable for a wide range of food products, including packaged goods, bulk products, and raw materials. 9. User-Friendly Operation: Modern conveyor metal detectors are equipped with user-friendly interfaces and advanced technology, making them easy to operate and maintain. 10. Ongoing Support and Service: Many manufacturers and suppliers of conveyor metal detectors offer ongoing support, training, and service to ensure optimal performance and reliability.
Choosing the Right Conveyor Metal Detector for Your Operations
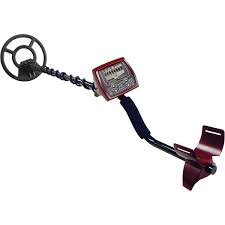
When selecting the right conveyor metal detector for your operations, it is important to consider factors such as the type of products being inspected, the size and weight of the products, the speed of the production line, and the level of sensitivity required. Different types of conveyor metal detectors are available, including aperture style detectors and tunnel style detectors, each with their own advantages and limitations. It is also important to consider the integration of the metal detector with the existing production line and the ease of maintenance and cleaning. Consulting with a knowledgeable supplier or manufacturer can help you make an informed decision about the best conveyor metal detector for your specific needs.
The Importance of Regular Maintenance for Conveyor Metal Detectors
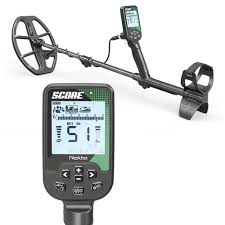
Regular maintenance for conveyor metal detectors is crucial for a variety of reasons. By ensuring that the detectors are regularly maintained, you can prevent equipment failure, reduce downtime, and extend the lifespan of the equipment. Regular maintenance also helps to maintain the accuracy and reliability of the detectors, which is essential for maintaining product quality and safety. Neglecting maintenance can result in decreased sensitivity and efficiency, leading to potential safety hazards and product contamination. Overall, the importance of regular maintenance for conveyor metal detectors cannot be overstated, as it directly impacts the effectiveness and efficiency of the production process.
Enhancing Food Safety with a Conveyor Metal Detector System
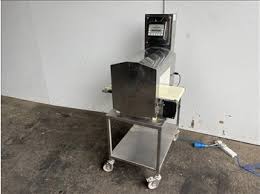
A conveyor metal detector system is an essential tool in enhancing food safety in manufacturing and processing facilities. These systems are designed to detect metal contaminants in food products as they pass along a conveyor belt, ensuring that contaminated products are removed from the production line before reaching consumers. Conveyor metal detector systems use advanced technology to accurately identify and reject metal contaminants, including ferrous, non-ferrous, and stainless steel particles. This helps to prevent potential harm to consumers and protects the reputation of the food producer. In addition to providing an extra layer of protection against foreign objects in food products, conveyor metal detector systems also contribute to compliance with industry regulations and standards for food safety. They can be customized to suit the specific needs of different food products and production environments, offering a reliable and efficient solution for ensuring product safety. Overall, the use of a conveyor metal detector system plays a crucial role in minimizing the risk of metal contamination in food products, ultimately enhancing food safety and consumer confidence.
Understanding the Different Types of Conveyor Metal Detectors
Understanding the Different Types of Conveyor Metal Detectors: 1. Balanced Coil Metal Detectors: These detectors use two coils - a transmitter coil and a receiver coil - to detect metal objects. When metal is present, it disrupts the magnetic field, causing a disturbance that is detected by the receiver coil. 2. Digital Metal Detectors: These detectors use advanced digital signal processing technology to accurately detect metal contaminants on a conveyor belt. They offer high sensitivity and can distinguish between different types of metal. 3. Multi-Zone Metal Detectors: These detectors are equipped with multiple detection zones, allowing for more precise identification of metal contamination. They can pinpoint the exact location of metal objects on the conveyor belt. 4. Pulse Induction Metal Detectors: These detectors are ideal for detecting metal in conductive products such as meat and dairy. They use short bursts of high-powered magnetic fields to identify metal contaminants. 5. Ferrous Metal Detectors: These detectors specifically target ferrous metals such as iron and steel. They are commonly used in industries where non-ferrous metals are not a concern. Understanding the different types of conveyor metal detectors is essential for selecting the most suitable option for your specific application. It is important to consider factors such as the type of product being inspected, the sensitivity required, and the environmental conditions in which the detector will be operating.
How Conveyor Metal Detectors Improve Efficiency and Productivity in Manufacturing
Conveyor metal detectors improve efficiency and productivity in manufacturing by automatically detecting and removing metal contaminants from the production line. This helps to prevent damage to machinery and products, reduces downtime for maintenance and repairs, and improves overall product quality. By quickly identifying and removing metal contaminants, manufacturers can avoid costly product recalls and ensure that their final products meet safety and quality standards. Additionally, the automation provided by conveyor metal detectors streamlines the production process, allowing for faster throughput and increased productivity. Overall, the implementation of conveyor metal detectors can lead to significant cost savings and improved operational efficiency in manufacturing facilities.
Maximizing Conveyor Metal Detector Performance with Proper Calibration
Maximizing conveyor metal detector performance with proper calibration involves ensuring that the detection system is set up according to the manufacturer's specifications. This includes adjusting the sensitivity levels, tuning the frequency, and calibrating the reject mechanism. Proper calibration is essential for accurate and reliable metal detection, as it helps reduce false alarms and missed detections. Additionally, regular calibration and maintenance are necessary to keep the system functioning optimally and to meet industry quality standards.
Troubleshooting Common Issues with Conveyor Metal Detectors
- Ensure that the metal detector is powered on and the settings are properly configured for the specific application. - Check for any electrical issues such as loose connections, damaged wiring, or faulty parts that may be causing the metal detector to malfunction. - Inspect the conveyor belt for any debris or foreign objects that may be interfering with the operation of the metal detector. - Evaluate the position and alignment of the metal detector to ensure that it is accurately detecting metal contaminants as intended. - Calibrate the metal detector according to the manufacturer's guidelines to ensure that it is functioning within the specified parameters. - If the metal detector continues to experience issues, contact the manufacturer for technical support and potentially schedule a service visit for professional maintenance.
Integrating Conveyor Metal Detectors into Existing Production Lines
Integrating conveyor metal detectors into existing production lines involves careful planning and implementation to ensure seamless operation. It requires assessing the layout and flow of the production line to determine the most suitable location for the metal detectors. This integration may also require modifications to the conveyor system to accommodate the detectors. Additionally, considerations such as product size, speed of the conveyor, and the type of metal detector technology must be taken into account to effectively integrate them into the production line. Proper calibration and testing are essential to ensure accurate detection without disrupting the production process. Overall, integrating conveyor metal detectors into existing production lines requires comprehensive understanding of the production environment and expertise in equipment integration.
Comparing Conveyor Metal Detectors to Other Food Safety Solutions
Comparing conveyor metal detectors to other food safety solutions, it is important to consider the specific needs and requirements of the food production facility. Conveyor metal detectors are able to detect metal contaminants in both packaged and unpackaged food products as they are transported along a conveyor belt. This makes them a versatile and efficient option for quality control in food production. Other food safety solutions, such as X-ray inspection systems, may offer additional capabilities, such as the ability to detect other types of contaminants, including glass, stone, and bone. However, these systems may also come with a higher initial cost and require more frequent maintenance. Chemical and microbiological testing are also important components of food safety, but these methods do not provide real-time, in-line detection of physical contaminants. In comparison, conveyor metal detectors offer a non-invasive and efficient way to identify and remove metal contaminants from the production line, helping to ensure the safety and quality of food products.
In conclusion, the use of conveyor metal detectors plays a vital role in enhancing industrial safety by preventing the contamination of products with metal particles and ensuring a safe working environment for employees. With advanced technology and reliable performance, conveyor metal detectors are an essential tool for industries to maintain high safety standards and prevent potential hazards. Therefore, implementing conveyor metal detectors is a necessary measure to improve industrial safety and safeguard the well-being of workers and consumers.
See also
https://detecteur-manche.com https://pro.mr-bricolage.fr